Practical engineering philosophy
Make sure no one dies.
Win funding.
Pass certification.
Professional sales content.
tomassab@gmail.com,
+45 50105868
Another potential disaster prevented.
SAVINGS greater than my work cost.
The client is absolutely fantastic. Wish I had more spare time for such “side projects”. Can only afford 4 to 8h per week… but… it has an impact.
The foundations need to hold 172 kNm loads at minimum… but, they hold… 13 kNm, not 172 kNm…
Foundations were found 10x weaker than needed. And yes, a working solution I know already… But the really fun part is we can reduce the cost of metal by 2000kg, by replacing some HEB300 with HEB180…
That way, the client already saves 5x what my services cost… purely in material savings…
Oh, and a preliminary roof design was done in 2h also… not the final, but… close enough, to estimate weight and so forth…
All in all, less than 12h to design a custom roof within more than a reasonable range of design.
This factory floor, with unique testing foundations for heavy machinery was the most painful project yet… it cost me my sanity. But - worked out good.
First, people were hell bent to build bridges that do not hold 1/10th of the load applied on them (heaviest industrial forklifts on the market). They insisted “cracks are overrated” and there should be no rebar in concrete… Tried to put brick, to support 30t loads on liquid mud…
Pull with 20t force, on a 200kg block… For a year I was lied to “we will just build now”… just build… now… Holding back the money, threatening to fire me - if I refuse to “prevent death for free”… A lot of overtime went into this… just to PROTECT them from themselves…
They ignored all my numbers. Shouting “don’t touch, don’t check”… 1h, 1h… we give you 1h!… and every piece that I checked - against orders - was red. Disastrously far from a working solution… disastrously… 10x… 5x…
It was an absolute, industrial scale disaster waiting to happen. And they would neither “learn” or “allow to do proper” math… refuse to plan… refuse to work together… ignore… not respond for months… It was going completely off the rails, taking my sanity together with it. I tried everything… But… In a desperate moment, I contacted the correct person (again, against orders not to).
Management was changed. Someone finally looked at the proof, numbers.
Real deadlines were communicated. Simulations done. Design complete. In extreme conditions, extreme deadlines. But… I didn’t recover. It took the life out of me… this treatment… the arrogance, ignorance… the fake illiterate leadership. They are so dangerous. It’s absurd.
Absurd beyond belief… unbelievable… some “happy la la land”… insane… but… once “the dads” noticed, a good outcome was achieved. Even if it cost me my mental health in the end. It was worth it… not only for “protecting the important people from killing their factory” - but for protecting the workers, who will be hired to work there…
Especially big thanks to the guys on the floor. I worked in warehouses myself, 15 years ago… started there. I know how humiliating and intimidating and irritating it is to be forced to “obey stupid orders”… So, now, as a certified university professor in engineering, I am trying hard not to “push” anyone. I’m used to educating “guys like me” - and the guys on the floor enjoy learning things. And we take our time to make sure we understand “why” something needs to be done… once we agree - fewer errors are made… and if someone brings good reasons - we avoid doing nonsensical “details” also…
Because they are smart, curious, caring, ambitious… not “asleep in a comfy chair”… we can cut down on drawings substantially - saving months on documentation due to extremely good communication… small sessions of “academic sparring” save months of work for everyone.
Good communication allows to let people “fill some gaps”. Reduces errors. Increases speed. Often avoiding excessive drawings (I check if it is correct, but… I trust them beyond what they are used to). I do not like giving “orders”. I insist - reason is the way forwards… And the 12 years of learning and then teaching advanced engineering topics at a University - are very useful for making “short exams”. It allows to recognize relevant competences. And synchronize work of large volumes of people. In… large and small projects. According to the unique, individual skills, needs, ideas…
I check if a person is really ready. It was my job for a decade to certify engineers. And… A+ to all the hard workers. The weekends of work are not only mine in this project. And I try to make sure - they are paid for not only their “hands” but intellectual property also. Thank you - for being smart and devoted. You rescued the project. And especial thank you to P.J… who had the spine to push back, and do things correctly… and above all, the wisdom, to communicate like a real human communicates to a real human being. Taking some “pressure” off, and bringing some quality - into the process. :)
AS7502 - Australian railroad standard is very clear about what loading conditions the structure has to be tested for.
And there is pretty much no other option, other than using FEM, to verify all the welds, pins and bolts for all of the loading cases.
The chassis has to be fatigue safe. And they no longer allow to certify things based purely on “physical test” results. Numbers must be provided.
It is not a big job. A few weeks for the numbers and simulations… and then a few back and forward messages with the certification office. But you have to allow the engineer to do his job. Without “blocking” the communication chain with excessive management…
The fastest and cheapest way is to do it right - on the first try…
The extra bonus is - the simulations and fast calculations generated FUNDING. The reviewers could see the thing will pass eventually, the clients stopped threatening they will cancel - ship back all 50 units… time to do the job was financed.
EN 51115 - is my favorite example of a “weaponized” standard.
A potential client approached me to design the spring for a railroad stopper - bumper. After looking at it for 20h, running the numbers and simulations, I found that they will be forced to use a special type of steel, which seems to be manufactured only in Germany. I’m holding the required geometry to myself for now…
The spring will need to have a special profile (square), it will need to be custom rolled, and then pre-stressed. There is no way to satisfy the requirements of EN51115 - in any other way. The standard is calibrated to precisely restrict the size of the component, to make the diameter of the spring small enough, to force you to use one of the highest strength, extremely rare grade of machining steel on the planet.
So… if they can afford the most expensive steel and a custom built factory for it. They probably are able to pay the “real money” - to the engineer who can design the whole factory, all the procedures AND the product.
The product is now in Sweden. And keeps selling / working. I was called in an emergency, when the original concept catastrophically failed, bent in half, touched the floor (and 3 months of 3 people time were wasted).
It took 1 week to find a solutions, 1 week to get it ready for manufacturing, and 1 week to manufacture. 3 weeks total - from concept to a working product. EN1993 + fatigue resistance, and a complex loading history.
The result:
less weight (30% less material).
More strength (3x stronger).
Faster to manufacture (less than 1/2 time to manufacture compared to the “original”: less welds, less bolts, less plates)
As a Bonus - early drawings used to recover confidence of the client’s client. Secure extra funding - to get the job done.
During review of the full product - the Rear Under Protection (RUPD) was put into question by reviewer. And they were correct.
It took another 5 days to verify and solve the detected problems. Advanced simulations required - sequential damage accumulation, in aluminum beam (a car crash test!). And - Success. The heavy truck is now on the road, certified… it is safe and it works well :)
Winch was tested. 20t - holds.. all the angles, slider positions, attachment points, internal load distribution... verified. And corrected by Tomas Sabaliauskas (me).
62h. The solution requires to observe interaction between 6 components... and the full pallet of FEM simulations. The drawings were provided "manufacturing ready", so had to be back-processed, modified and re-built...
8h. Yoke for 20t pull. Residual stresses and weld stresses verified. Strict warning given that the yoke is not fatigue safe... but will not fail "instantly". The joint is complex in behavior, surface contacts and complex welds... can be done safely, though.
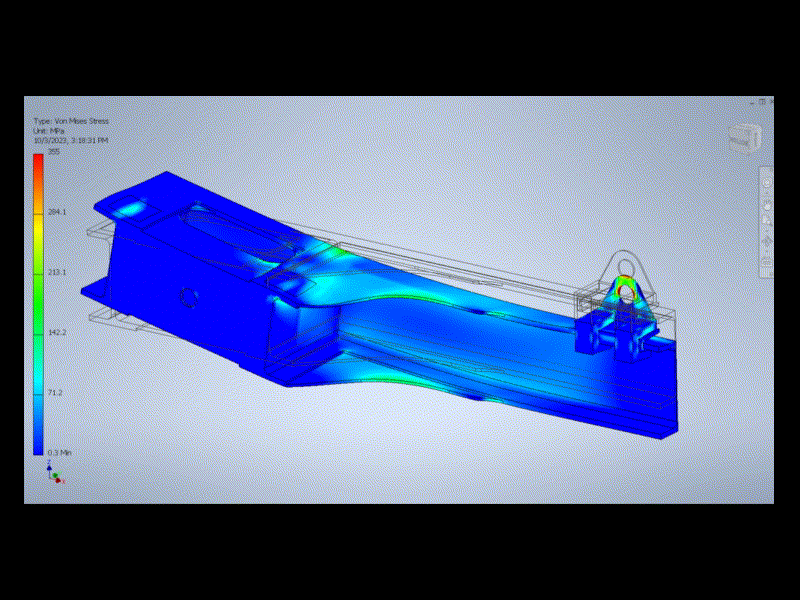
12h. 30t pull, creating 1MNm of overturn... this beam is fully fatigue safe. And the "sliding hooking point" makes operation extra convenient.
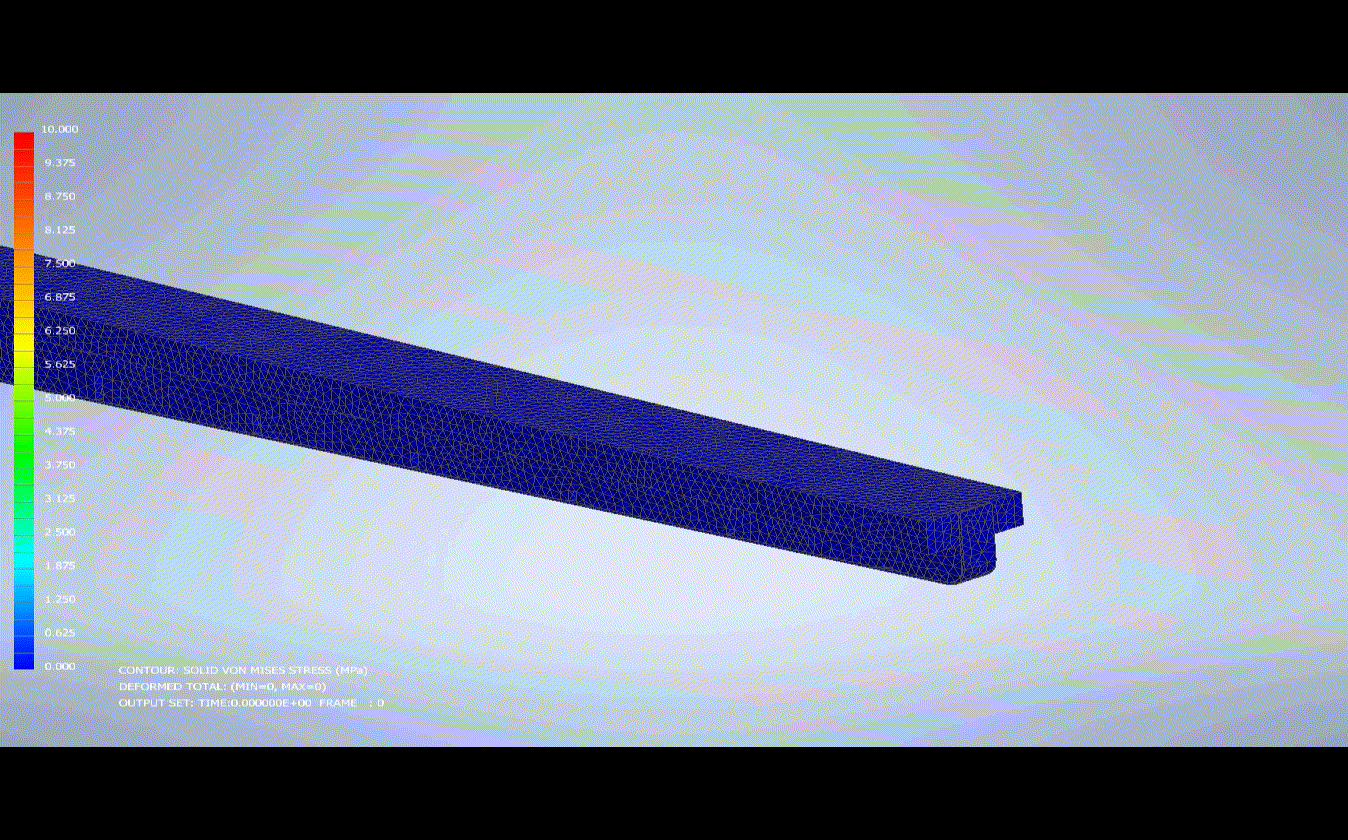
16h - custom / experimental / unique reinforced concrete bracing is a nightmare... but... it can be attempted. This is a "research grade" task, which normally asks for many months of funding, but... not if you "rent the scientist", directly.
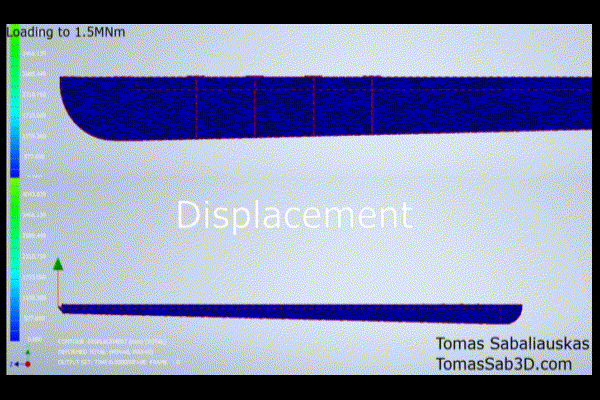
30h simulation- this beam explodes in the simulation, but would probably hold in real life practice (according to Eurocodes). The advanced simulations make extremely safe structures. If it holds in numerical - it will hold in reality.
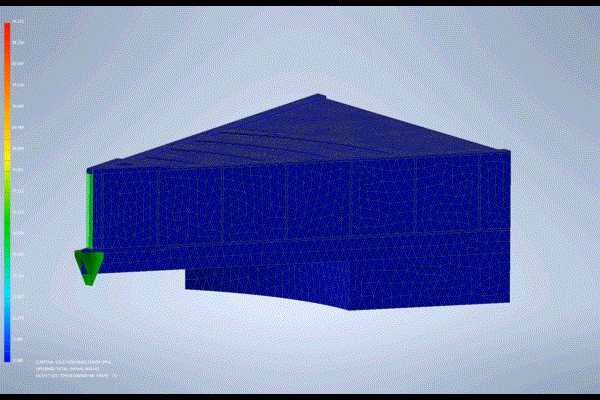
16h - "cage" reinforced concrete. This will hold, guaranteed. Many would argue it's overkill, but... if it breaks, you can't fix it. Even with exaggerated crack sensitivity this one is holding. Therefor, I'd approve it for manufacturing / testing.
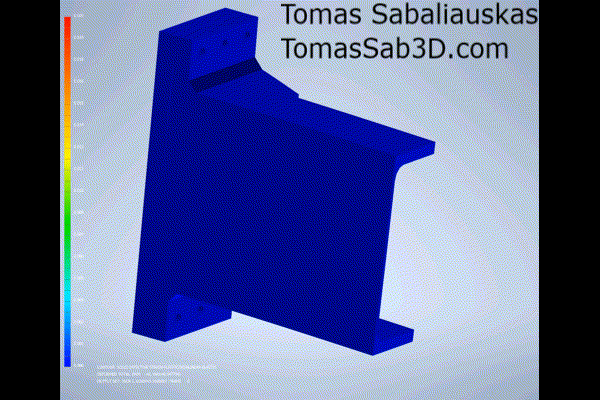
1 day. Bolted joint. Fatigue safe test... it will hold min 500 ULS cycles... EN3 compatible. The bolts make it plausible to transport the structure, avoiding on the field manufacturing.
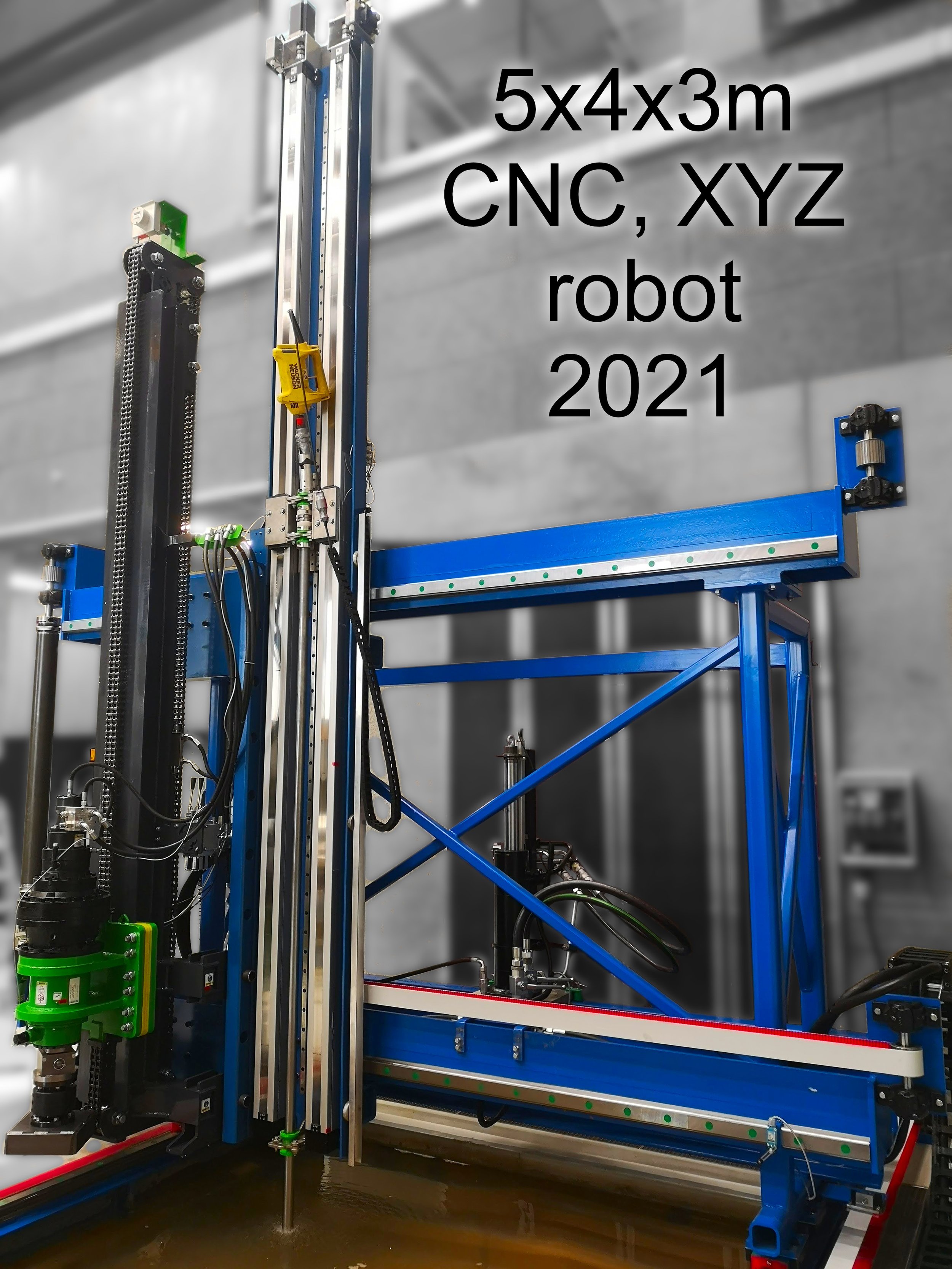
6 weeks - 2tonnes heavy, 5m tall CNC machine. Design time... safe down to last bolt, wire, beam and linear actuator. Industrial offers asked 10x more expensive components and 10x more money... very annoying. Push down force - 250kN, torque capacity 50kN, unique anchors to concrete and unique water supply system on the bottom of the sand box. 3 years in operation - no problems so far. Not even once.
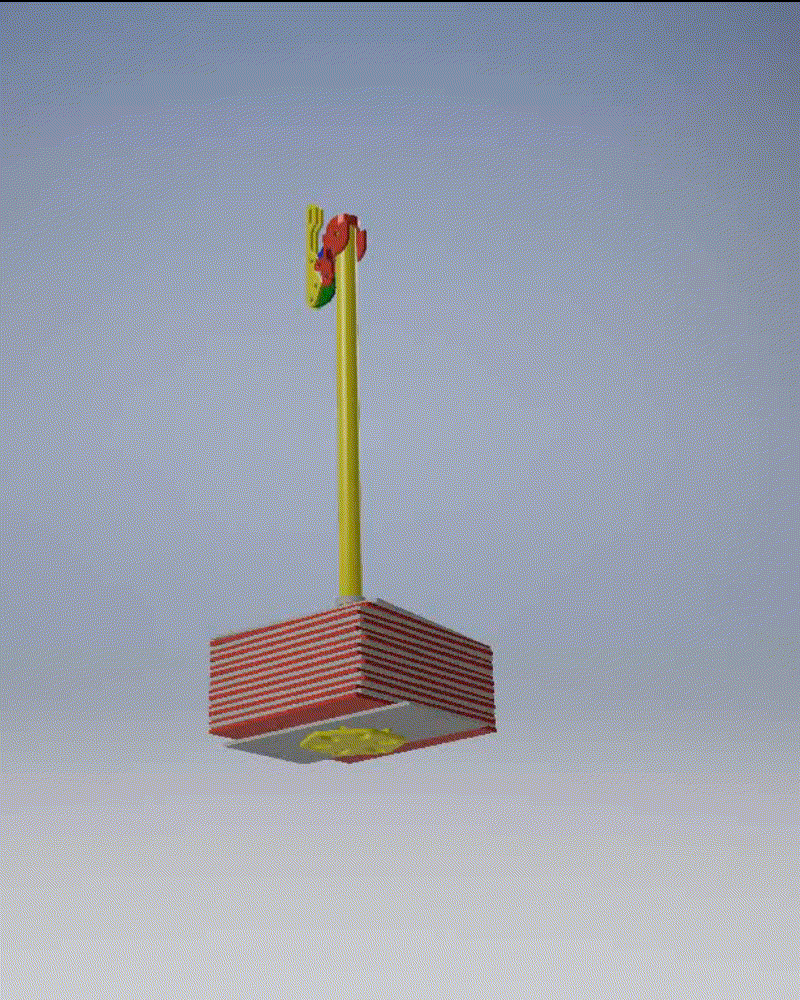
36h - A mechanical hammer for field testing. With precision controlled release mechanism, and double safety features (patented). Pull force - 5kg max. Load - 500kg. Drop height adjustable. 2 years in operation - no problems.
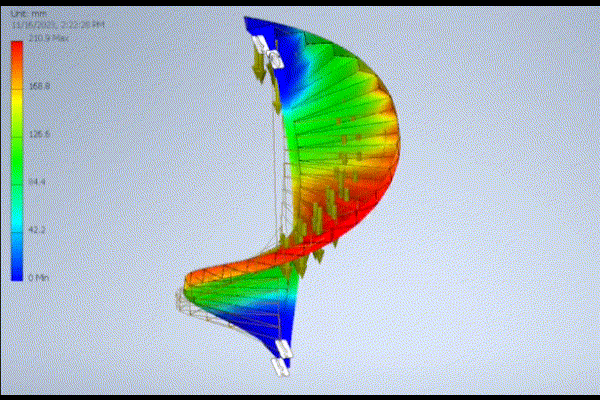
In 6h, helical the stairs were drawn, and validated. These could be welded from S355 and remain: 1. Fatigue safe 2. Feel stable (not "shaky"). 3. Certifiable for CE mark.
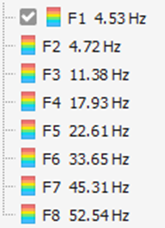
Natural frequency depends on how the stairs are attached. The way stairs are anchored has a big impact on their ergonomic performance. And safety... wrong connection will conflict with EN requirements (any mode below 10Hz is not good, and added mass during operation must be considered).
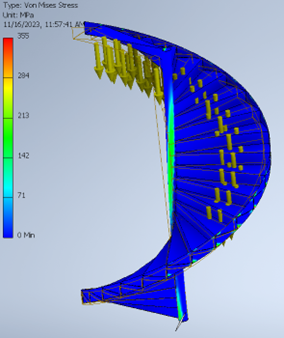
Stress in ULS case of overloading... within fatigue limits.
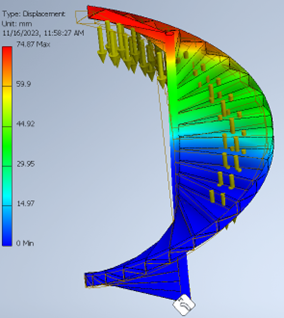
Displacements...
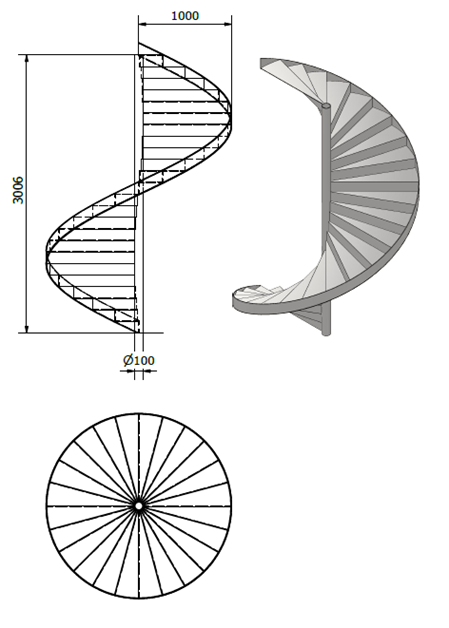
Obviously manufacturing / production drawings are easy to generate... it is rather obvious, but at times needs to be mentioned.
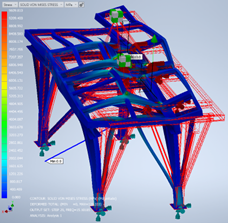
Frame dynamic response is important when attaching sources of vibration - like engines, and moving parts. In this case a client wants to replace a 1.5t mixes with a 5t mixer.

The frequency response analysis shows high risk of resonance and the frame has to be modified.

Tuned mass dampers are Calibrated, and attached.
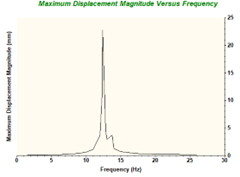
The resulting response shows the solution is adequate. Total work time - 24h... The tuned mass dampers can be designed in numerous ways. Best to use industrial components... but, I can make preliminary design of pneumatic and hydraulic components too.
Thermal analysis
PED (Pressure equipment directive) asks for numbers. Numbers must be made for:
operation pressure
design pressure (+fatigue +thermal)
Test pressure
Rupture pressure
EN13445 is one of my favorite standards, because low risk containers are fully FEM compatible to certify :)
Also - it is often plausible to remove 70% of manufacturing operations, and increase manufacturing speed by 4x, while reducing weight of a structure… when it is optimized, by a professional.
The project where my numbers produced CE marking for American clients - are NDA. Non disclosure agreement. So I attach a demo version here of what it looks like to investigate a heat exchanger :) Furnaces, pyrolysis stations… all those are fascinating. Stainless steel, SS316L is a fantastic material… doesn’t harden when welded. Super reliable.
Managing the tasks - is best done by the person who “does the tasks”. All managers do is ask “how long will it take”. So, if you do not work on 4 projects at once - you can do without having 4 managers on top of 1 worker.
Experience, intuition - provide realistic time estimates. Within 10% precision. That can be done without 500% “overhead” cost.
Less hours - allowing the person who “does the job” to “pick the tools and the people”. Effective + efficient.
Less people - a person with “fundamental knowledge” of material properties and manufacturing processes is able to calibrate simulations and do the numbers for LARGE VARIETY of materials. International standards… which means you DO NOT NEED 4x and 16x more people, different “specialists” for “different tasks”. Physics is all the same. And material models - differ only in parameters for 95% of all problems…
Combining the two : fundamentals of physis + work experience - allows to do things substantially faster… this “fair play” approach, allowing “the one who knows to do what he knows how to do” consistently produces 16x lower cost. Reliable. And budget friendly.
Consult with the engineer, a real engineer… the solution finder…
save yourself >1600% of “overhead” cost…
Small / silly hobby projects.
More experience, more ideas…
-
Chocolate - business card
-
Bird Feeders
-
Custom attachments
-
Custom tool hangers
-
Custom molds
-
Flexible components
-
Sensor mount
-
Random experiments
-
High temperature strength
For more examples visit my YouTube channel.
Tomas Sabaliauskas, TomasSab@gmail.com, +45 50105868